What is Aluminum Extrusion?
Aluminum extrusion is a manufacturing process that involves shaping aluminum alloys by forcing them through a die with a specific cross-sectional profile. The process begins with a heated aluminum billet or log, which is then loaded into the extrusion press.
Inside the press, the billet is pushed through the die, which gives the aluminum its desired shape and size. The die can have various shapes and sizes, depending on the specific application and end-use requirements of the extruded product.
The resulting extruded aluminum profiles can be used in a wide range of industries, such as construction, transportation, and electronics, to create various products like window frames, doors, curtain walls, heat sinks, and more.
The benefits of aluminum extrusion include its versatility, strength, and lightweight properties, making it an ideal material for various applications that require high-performance parts with intricate geometries and cross-sectional profiles. Additionally, aluminum extrusion is a cost-effective and sustainable manufacturing process that generates minimal waste and has a low environmental impact.
Our Aluminum Extrusion Processes
Aluminum extrusion is a manufacturing process that involves shaping aluminum alloys by forcing them through a die with a specific cross-sectional profile. Here's how to extrude aluminum:
-
Design the extrusion: The first step is to design the extrusion, which includes determining the desired shape, size, and profile of the final product.
-
Prepare the aluminum billet: The aluminum billet is typically made by casting or forging aluminum alloy into a cylindrical shape. The billet is then heated to a specific temperature, usually between 400 and 500 degrees Celsius, to make it easier to extrude.
-
Load the billet into the extrusion press: The heated billet is loaded into the extrusion press, which consists of a chamber with a piston that can push the billet through the die.
-
Extrude the aluminum: The billet is then pushed through the die using the press, which shapes the aluminum into the desired profile. The extruded aluminum is then cooled, either by air or water, to maintain its shape.
-
Cut the extrusion to length: The extrusion is then cut to the desired length using a saw or other cutting tool.
-
Finish the extrusion: Depending on the specific requirements of the extruded product, finishing techniques like CNC machining, welding, and surface treatment may be applied to the extrusion.
Advantages of Aluminum Extrusion
Aluminum extrusion offers several advantages over other manufacturing processes. Here are some of the main advantages of aluminum extrusion:
Aluminum extrusion can produce a wide range of shapes and sizes, from simple to complex geometries, with tight tolerances and uniform cross-sections.
Aluminum extrusion is a cost-effective manufacturing process, especially for high-volume production runs, due to its efficiency and repeatability.
Aluminum extrusions are lightweight and have excellent strength-to-weight ratios, making them ideal for applications where weight reduction is critical, such as in the aerospace and automotive industries.
Aluminum extrusions are naturally corrosion-resistant and can be further enhanced with surface treatments like anodizing, painting, or powder coating.
Aluminum is a highly recyclable material, making aluminum extrusions a sustainable and eco-friendly option.
Aluminum extrusions can be easily machined, drilled, and cut to fit specific design requirements, making them suitable for a wide range of applications.
Applications of Aluminum Extrusion
Aluminum extrusions are used in various construction applications, such as windows, doors, curtain walls, railings, and structural components.
Aluminum extrusions are used in the automotive industry to make lightweight, high-strength components like engine blocks, body frames, and suspension systems.
Aluminum extrusions are commonly used in the aerospace industry to make aircraft frames, landing gear, and other structural components.
Aluminum extrusions are used in electronics applications such as heat sinks, frames, and enclosures due to their lightweight and excellent thermal conductivity.
Aluminum extrusions are used in renewable energy applications like solar panels and wind turbines due to their lightweight and corrosion-resistant properties.
Aluminum extrusions are used in transportation applications such as bicycle frames, marine equipment, and railway cars due to their high strength-to-weight ratio and resistance to corrosion.
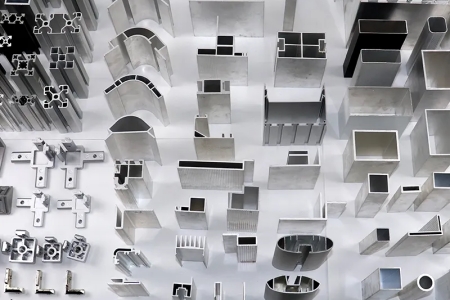
Finishing Options for Aluminum Extrusion
Aluminum extrusions can be finished in a variety of ways to enhance their appearance, improve their corrosion resistance, and increase their durability. Some common finishing options for aluminum extrusions include:
-
Anodizing
-
Powder coating
-
Painting
-
Polishing
-
Brushing
-
Sandblasting
Why Comely CNC?
• Streamlined process flow
At Comely CNC, our operations follow a dedicated process flow that minimizes risk, verifies raw materials, and ensures the production of high-quality prototypes and end parts consistently.
• Quick turnaround
Leverage our industrial-grade equipment to accelerate your product development cycles and hasten your time-to-market. With our expertise, we can help you overcome bottlenecks and fast-track your product development right away.
• Scalable and consistent manufacturing
Our additive manufacturing solutions prioritize scalability and repeatability, providing you with the flexibility to prototype or manufacture according to your budget without compromising quality.
• Comprehensive finishing services
In addition to our precision printing capabilities, we also offer finishing solutions to enhance the aesthetic appeal of your parts. Our in-house finishing services are subject to the same stringent quality control measures for a lasting guarantee of quality.
• Quality and Consistency
We prioritize quality throughout the production process, ensuring consistent, high-quality end-use products.
• Cost and Profitability
Our competitive pricing adds value to client's businesses by delivering parts at a lower cost-per-part, making us one of the most competitive manufacturing businesses in China.
• One-Stop Shop
Our one-stop-shop approach streamlines the product development cycle, providing comprehensive services from design to finishing solutions that enhance the appearance and functionality of the final product.