Molded silicone foam parts are specialized components made from silicone rubber that incorporate a foaming process during manufacturing. These parts are designed to provide unique properties and applications compared to solid silicone components. Molded silicone foam parts find applications in various industries, including automotive, aerospace, electronics, healthcare, and consumer goods. Some common examples include gaskets, seals, vibration dampeners, padding, and insulation components.
The cellular structure of silicone foam parts allows for excellent compression and impact absorption properties, making them ideal for cushioning and shock-resistant applications. The foam also provides enhanced insulation against temperature, sound, and vibrations, which can be crucial in industries such as automotive and electronics.
Additionally, molded silicone foam parts exhibit good chemical resistance, UV resistance, and weatherability, making them suitable for outdoor and harsh environment applications.
The molding process for silicone foam parts can be tailored to achieve specific foam densities, hardness levels, and shapes to meet the requirements of different applications. This versatility allows for customization and precise engineering of the foam parts.
In summary, molded silicone foam parts are silicone rubber components with a cellular foam structure. They offer advantages such as reduced weight, cushioning, insulation, flexibility, and customization options. These parts find applications in various industries where lightweight, impact absorption, and insulation properties are required.
Specification
Place of Origin |
Guangdong,China |
Material |
100% Silicone |
Brand Name |
JE |
Processing Service |
Forming, Molding |
Temperature resistance |
-40~250 ºC |
Hardness |
10-50C |
Color |
customized |
Size |
customized |
Product Certification |
ROHS,ISO |
Packing |
according to the order |
Applications |
Aircraft/CO2/Food/Engine Seals |
Features
1. Excellent temperature resistance
2. Excellent UV resistance
3. Excellent ozone resistance
4. Extremely resilient to mechanical fatigue
5. Excellent flame resistance
6. Open cell at low densities
Product Images
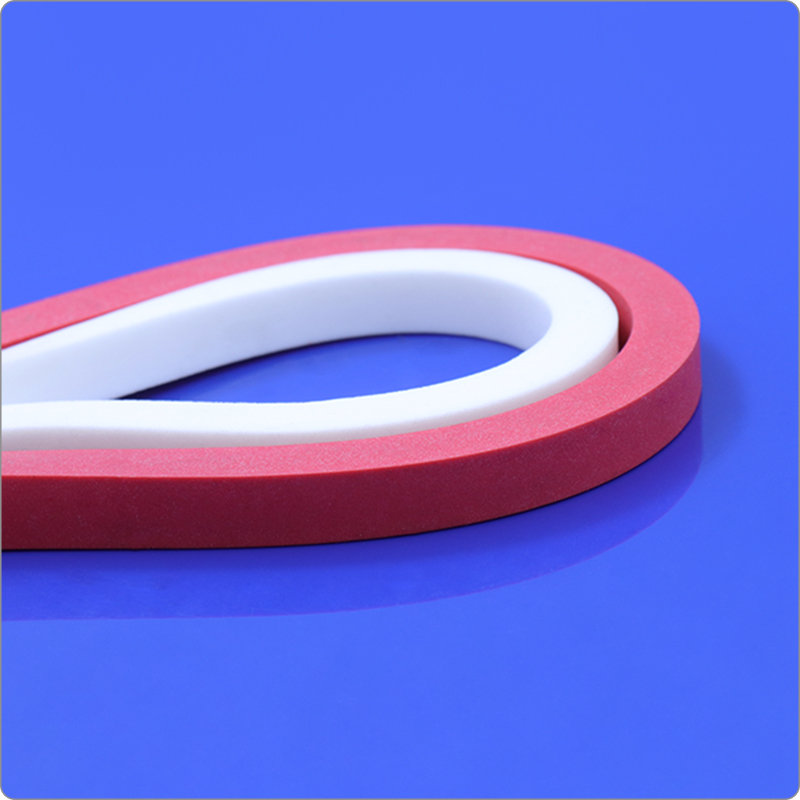
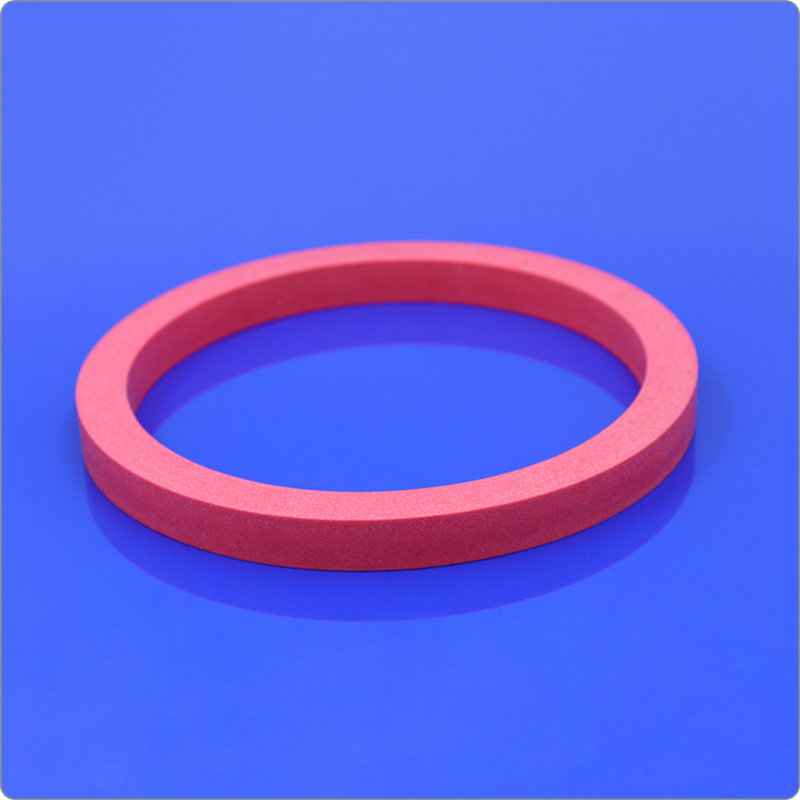
Our Factory
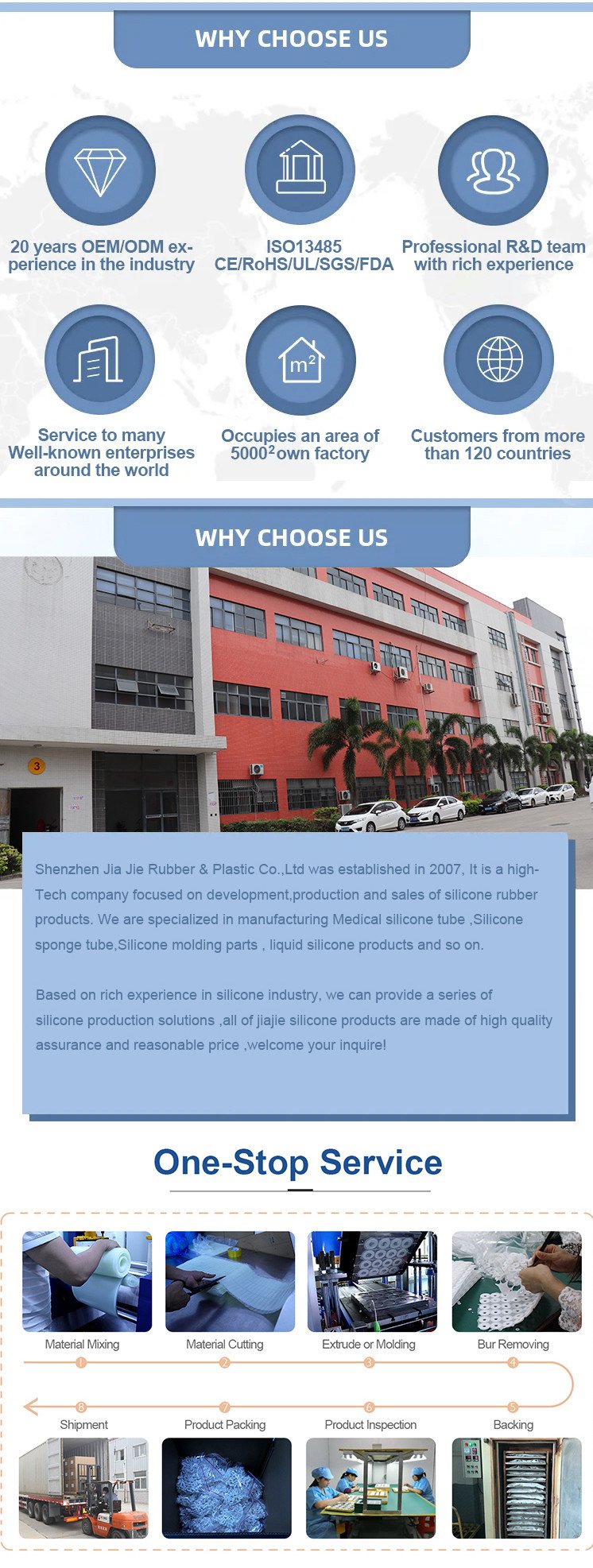
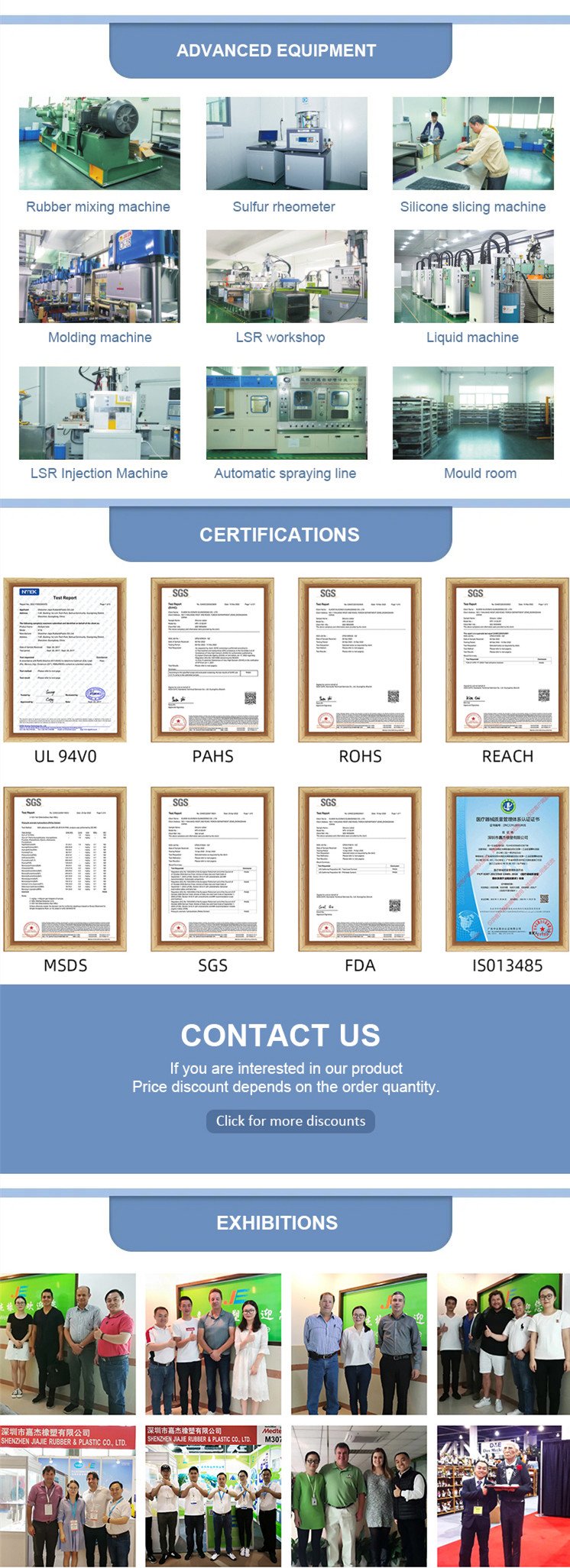