ZX210 Friction Welding Track Roller Yellow Color Bottom Roller
1. What's a Track Roller?
The track roller is an important part of undercarriage, it has two kinds of welding methods, one is traditional and the other is friction-welding.
2. Differences between Friction-welding and Traditional Rollers
-
Friction-welding track roller is better in the wear-resistance and has a longer working lifetime.
-
Consumption of raw material: the roller bodies of traditional track roller are connected by the welding rod. but the friction ones are connected by the friction between rollers' bodies. So the friction-welding roller will be added more raw material to make sure the roller is perfect to the standard size after welding.
-
Inner parts: For the traditional rollers, the welding is done after two processes of machining, so the size of the inner parts is not so precise as friction-welding ones. For the friction-welding ones, after the welding, there is one more precise machining with concentric locating to make sure the conformity of inner size, this means the inner parts are more precise with a higher standard.
3. Main Materials
Main body
|
50Mn/40Mn2 Alloy steel
|
Shaft
|
45# Alloy steel
|
Side cover
|
50Mn/40Mn2 Alloy steel
|
Bi-metal sleeve
|
CuPb10Sn10
|
Ring float
|
Cr16Mo2NiCu
|
Hexagon bolt
|
JB/T1000-1977 OEM
|
O-ring
|
High quality rubber
|
Lubricated oil
|
High quality 40#
|
4. Production Processes
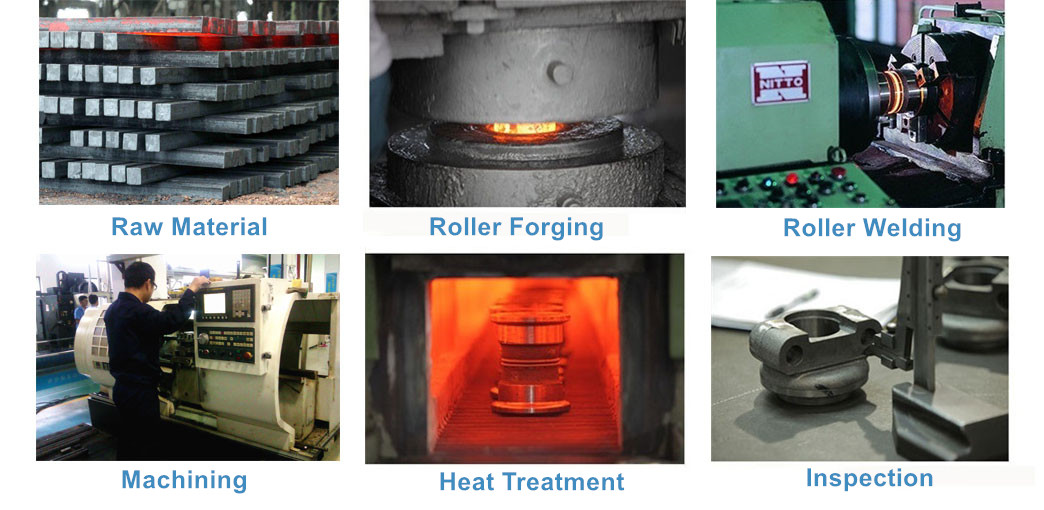
5. Why Choose Us?
• Advanced Germany KUKA automatic machining center, horizontal and vertical CNC machining ensure the accuracy of assembly dimensions. This is to maximize the life span of each component and minimize production cost.
• Each roller shell is carefully heat treated to ensure long wear life and stress resistance.
• Our heat-treatment process provides hardness in high wear areas, and elastic core to resist shock and impact loads.
• Strict quality management aims to produce effective and stable products, and meet customer's demand.
•The use of mechanical oil and environmental protection paint improves the ability to resist high and low temperature and extends the product’s working life under severe environment.
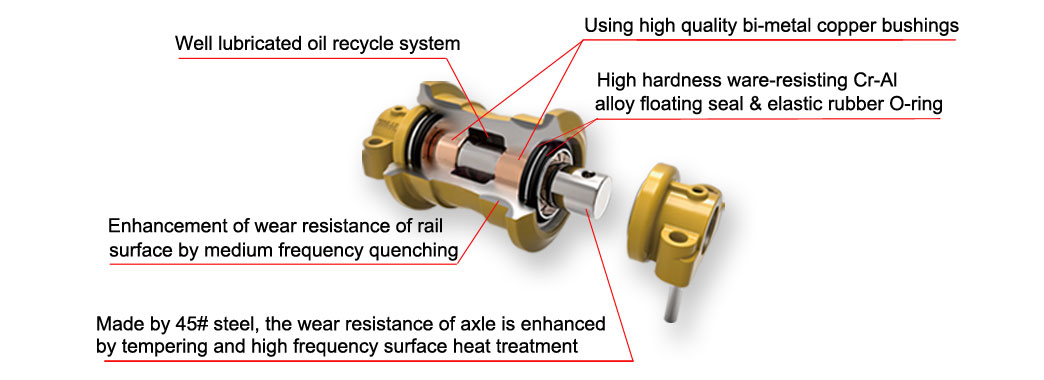
6. Tips for Track Rollers
-
Single and double-edge track roller suits for excavating machines and special machinery ranging from 3 to 50 tons.
-
Double conical sealing and lifelong lubrication designing enable the track roller to have a longer lifetime and perfect performance in any circumstances.
-
The shell made by hot forging treatment obtains the superior structure of internal materials and fiber.
-
Different quenching or feed-through quenching heat treatment is effective in crack resistance.