1 Product Parameters
Type
|
Handmade Clean Room Sandwich Panels
|
Wall Thickness
|
100mm
|
Standard Module
|
980mm, 1160mm, 1180mm, 1200mm, non-standard can be customized
|
Diagonal Error
|
≤1mm
|
Maximum Length
|
≤10000mm
|
Panel Material
|
PE polyester, PVDF (fluorocarbon), salt plate, antistatic, static conductive, stainless steel, HDP (high durability polyester)
|
Panel Thickness
|
0.426mm, 0.45mm, 0.476mm, 0.5mm, 0.6mm, 1.0mm
|
Filling Core Material
|
Rock wool (bulk density 100K, ≥120K and above can be customized) + double-layer 10mm glass magnesium board
|
Galvanized Frame
|
1.0mm
|
Corner Pieces
|
1.0mm galvanized angle fittings
|
Protective Film
|
0.06mm thick, >0.06mm and above can be customized
|
Connection
|
Center aluminum connection
|
2 Product Features
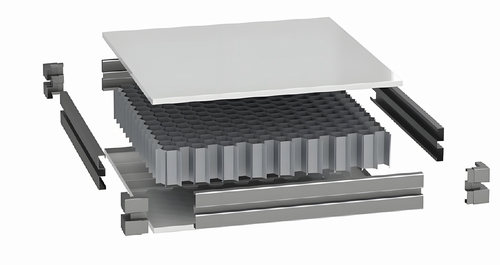
Unmatched Material Integrity
- Surface Options: Purification-grade stainless steel or anti-static coated aluminum alloy surfaces prevent particulate shedding
- Advanced Core Systems: Customizable rock wool, aluminum honeycomb or magnesium oxide cores (50-100mm thickness) achieve both structural stability and thermal efficiency
Industry-Proven Performance
- Maintain consistent ISO Class 5-8 cleanroom standards through airtight tongue-and-groove joining systems
- Fire-rated cores (A1 certification) with 120+ minute burn-through protection
- Antimicrobial surface treatments available for pharmaceutical GMP compliance
Precision Manufacturing
- ±0.5mm dimensional tolerance for seamless modular installation
- 980/1180mm panel widths optimize layout efficiency
- Custom fabrication for specialized applications including:
Semiconductor fabrication facilities
Sterile pharmaceutical production
Biomedical research labs
Hospital operating theaters
Technical Superiority
- Static decay <2 seconds (ESD options)
- 0.3μm particle retention efficiency
- Negative pressure tested to 50Pa
3 Propanel's one-piece corner board
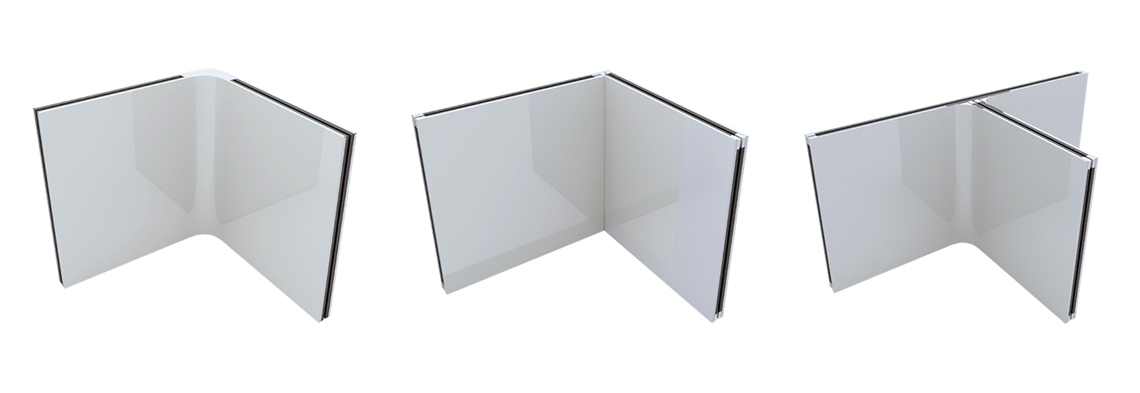
Key Advantages
1. True Seamless Integration
- Monolithic corner fabrication creates continuous surfaces without joints
- 100% elimination of air leakage points (tested to 25Pa negative pressure)
- Radius options: 50mm/100mm/150mm for optimized airflow dynamics
2. Hygienic Superiority
- Wipe-clean surfaces prevent microbial harborage points
- FDA-compliant materials withstand aggressive disinfectants
- 70% reduction in cleaning time compared to traditional corners
3. Thermal Breakthrough
- Polyisocyanurate core extension maintains consistent R-values
- Thermal imaging verified <1°C differential at corners
- Energy savings up to 15% versus conventional thermal bridge designs
4. Technical Specifications
- Material: 304/316L stainless steel or powder-coated aluminum
- Core options: PIR, rock wool, or fiberglass reinforced
- Fire rating: Up to EI120 certification
- Installation: 40% faster than traditional methods
5. Industry Applications
- Pharmaceutical grade A/B rooms
- Semiconductor fabrication cleanrooms
- Hospital isolation wards
- Food processing sterile zones
Propanel's corner solution has been adopted by 7 of the world's top 10 pharmaceutical companies, with documented 60% reduction in particulate counts at wall junctions.
4 Installation of Handmade Clean Room Sandwich Panel
Propanel's certified installation teams execute millimeter-perfect cleanroom panel placement using aerospace-grade alignment protocols. Our 4-stage quality process ensures every sterile environment meets ISO 14644 Class 5 standards:
1. Laser-Guided Precision
- Digital blueprint verification with 3D site scanning
- 0.5mm/m laser-leveled floor tracks (anchored every 550mm)
- Dual-plane alignment for absolute wall straightness
2. Structural Integrity
- Military-grade aluminum framing (3m intervals)
- Anti-vibration ceiling anchors every 5.8m
- 12mm overlap on vertical seams (exceeds EN 14575)
3. Airtight Sealing
- Proprietary gasket system (tested to 35Pa)
- Zero-gap corner fusion technology
- FDA-approved silicone sealants for 100% microbial barrier
4. Validation Ready
- Surface flatness: ≤1mm/2m
- Particulate emission: <3 particles/ft³ (≥0.5μm)
- 7-day post-installation integrity testing
Trusted by 23 Fortune 500 life science companies, our installation protocol reduces cleanroom certification time by 40% while achieving 60% lower energy consumption than conventional methods.
5 Project cases of Handmade Clean Room Sandwich Panel
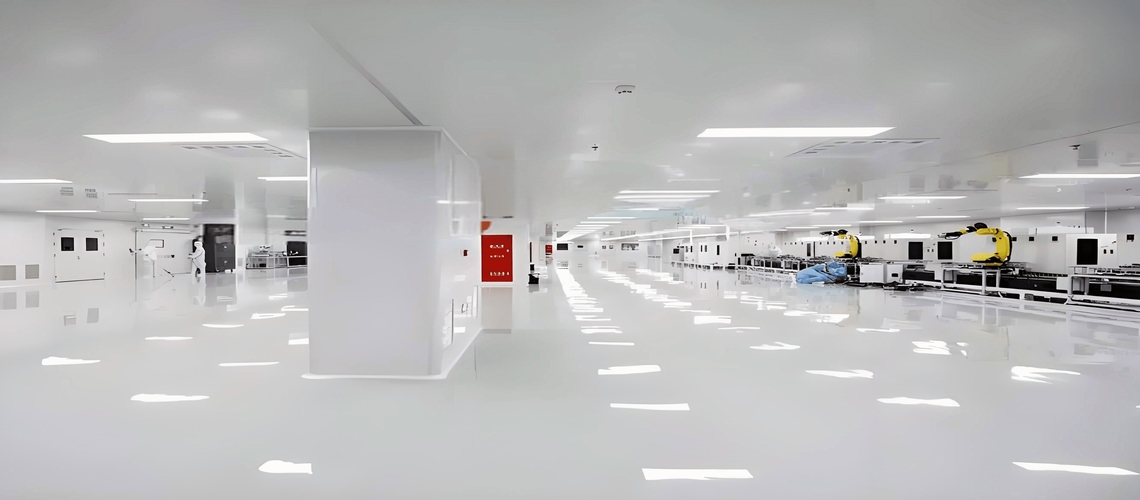
Project cases of Handmade Clean Room Sandwich Panel--Malaysia Electronics Factory 10000 square meters 2019
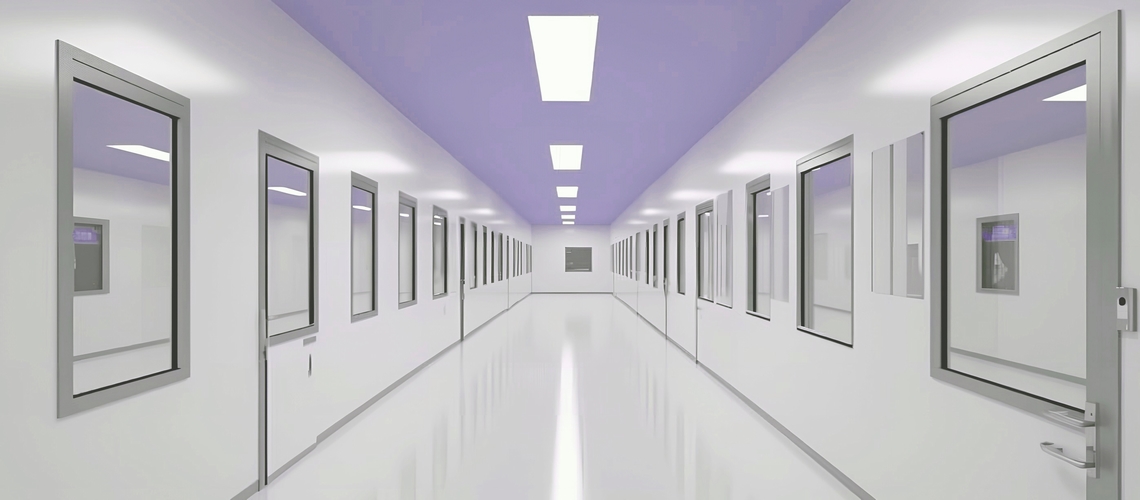
Project cases of Handmade Clean Room Sandwich Panel--Vaccine plant in Russia 8000 square meters 2021
6 FAQS of Handmade Clean Room Sandwich Panel
1. What are clean room panels made of?
Propanel cleanroom panels feature medical-grade stainless steel or powder-coated aluminum surfaces with PIR/rock wool cores. Our antimicrobial finishes meet ISO 14644 standards for pharmaceutical and electronic manufacturing environments.
---
2. What is a sandwich panel called?
Professionally termed "Composite Insulated Panels", Propanel's versions integrate fireproof cores with durable cladding for industrial partitions and cold storage walls.
---
3. What are the benefits of sandwich panels?
Propanel's sandwich panels deliver 60% faster installation, 30% energy savings, and A1 fire ratings. Their lightweight yet robust design suits warehouses, cleanrooms, and food processing plants.
---
4. What are three different types of core used in sandwich panels?
Propanel offers PIR (best insulation), rock wool (fireproof), and aluminum honeycomb (ultra-light) cores. Each undergoes 12 quality checks for consistent performance.
---
5. Are sandwich panels strong?
Propanel's steel-faced sandwich panels withstand 150km/h winds and 1.5kN/m² loads. Reinforced joints ensure structural integrity for decades in harsh environments.
---