Komatsu PC200 Friction Welding Track Roller
1. What is Friction Welding Roller?
The track roller has two kinds of welding methods, one is traditional and the other is friction-welding. Friction welding is a solid-state joining process, which could achieve reliable solder joints and create high-quality, high-strength joints with low distortion.

2. Differences between Friction-welding and Traditional Rollers
-
Friction-welding track roller is better in the wear-resistance and has a longer working lifetime.
-
Consumption of raw material: the roller bodies of traditional track roller are connected by the welding rod. but the friction ones are connected by the friction between rollers' bodies. So the friction-welding roller will be added more raw material to make sure the roller is perfect to the standard size after welding.
-
Inner parts: For the traditional rollers, the welding is done after two processes of machining, so the size of the inner parts is not so precise as friction-welding ones. For the friction-welding ones, after the welding, there is one more precise machining with concentric locating to make sure the conformity of inner size, this means the inner parts are more precise with a higher standard.
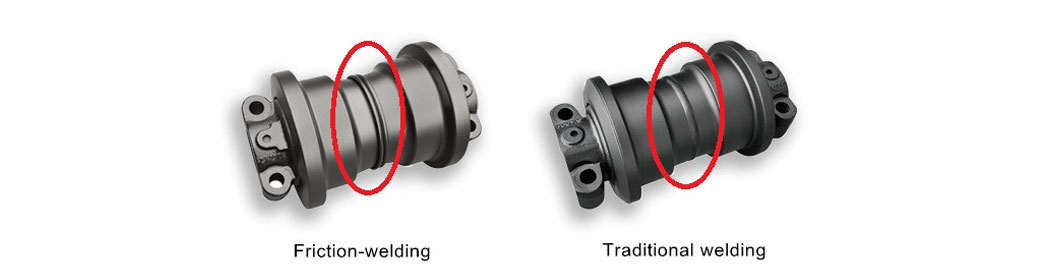
3. Why Choose Us?
-
Our track roller are
specially designed, engineered and manufactured for high impact applications.
-
We use good material to ensure quality and
consistency.
-
Each
roller shell is carefully heat treated to ensure long wear life and stress
resistence.
-
Our heat-treatment process provides
hardness in high wear areas, and elastic core to resist shock and impact loads.
-
Strict quality management aims to produce
effective and stable products, and meet customer's demand.
-
Reliable
and long life-time guarantee.
4. Manufacturing Processes
5. Tips for Track Rollers
-
Single and double-edge track roller suits for cater excavating machines and special machinery ranging from 3 to 50 tons.
-
Double conical sealing and lifelong lubrication designing enable the track roller to have a longer lifetime and perfect performance in any circumstances.
-
The shell made by hot forging treatment obtains the superior structure of internal materials and fiber.
-
Different quenching or feed-through quenching heat treatment is effective in crack resistance.