What is Plastic Injection Molding?
Plastic injection molding is a manufacturing process in which molten plastic material is injected into a mold cavity under high pressure. The molten plastic then cools and solidifies, taking the shape of the mold cavity, and is ejected as a solid part. This process is commonly used to produce high volumes of plastic parts with a high degree of accuracy, consistency, and surface finish. It is widely used in various industries, including automotive, aerospace, medical, and consumer products. Plastic injection molding is an efficient and cost-effective method for producing complex and intricate shapes and can be used with a wide range of plastic materials.
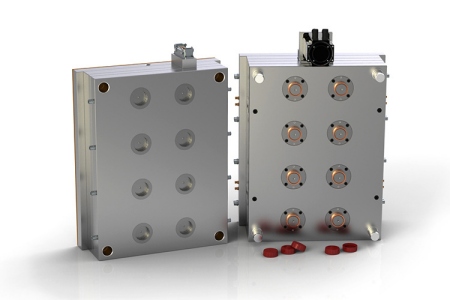
The process of making injection-molded parts typically involves several steps, including:
• Design the Mold:
The first step in the process is to design the mold that will be used to produce the plastic parts. This involves designing a 3D model of the part and the mold, and then creating a mold tool that can be used in the injection molding machine.
• Set up the Injection Molding Machine:
Once the mold is ready, it is mounted onto the injection molding machine, which consists of a hopper, a barrel, a screw, and a heating unit. The plastic pellets are loaded into the hopper and are then fed into the barrel.
• Melt the Plastic:
The plastic pellets are melted in the barrel using heat and friction from the screw. The molten plastic is then injected into the mold cavity under high pressure.
• Cool and Solidify the Plastic:
The plastic is allowed to cool and solidify in the mold cavity. The cooling time depends on the thickness of the part and the type of plastic used. Once the plastic has solidified, the mold is opened and the part is ejected.
• Finish the Part:
The part may need to undergo additional finishing processes such as trimming, polishing, or painting to achieve the desired final product.
• Repeat the Process:
The injection molding process can be repeated multiple times to produce a large quantity of identical parts.
Applications of Plastic Injection Molding
• Automotive Industry:
Injection molding is used to manufacture various automotive parts, such as bumpers, dashboards, interior panels, and more.
• Medical:
Injection molding is used to produce medical devices, such as syringes, tubing, and medical equipment components.
• Consumer Goods:
Injection molding is used to make products such as toys, kitchenware, packaging materials, and electronic device components.
• Aerospace:
Injection molding is used to manufacture aircraft parts such as seats, interior panels, and control components.
• Construction:
Injection molding is used to produce parts for building construction such as roofing tiles, pipes, and fittings.
• Sports and Recreation:
Injection molding is used to manufacture sports equipment like helmets, knee pads, and balls.
• Electronics:
Injection molding is used to produce components such as housings, switches, and connectors for electronic devices.
• Packaging :
Injection molding is used to produce packaging materials such as bottles, caps, and containers.
Why Should I Choose Injection Molding?
• High Production Efficiency:
Injection molding is a highly automated and efficient process that can produce large quantities of identical parts quickly and consistently.
• Versatility:
Injection molding can be used to produce parts in a wide range of sizes, shapes, and complexities, making it a versatile manufacturing process.
• Material Options:
Injection molding can use a variety of plastic materials, including thermoplastics and thermosetting polymers, allowing for a wide range of material properties and characteristics.
• Design Flexibility:
Injection molding allows for complex and intricate part designs with tight tolerances, making it an ideal process for producing parts with complex geometries.
• Cost-effective for Large Volumes:
Injection molding can be cost-effective for producing large volumes of parts, as the high initial tooling costs can be offset by the low cost per part produced.
• Reduced Material Waste:
Injection molding produces very little material waste, as any excess plastic can be recycled and reused in the process.
Why Comely CNC Injection Molding?
Take advantage of our professional injection molding services and produce top-tier quality parts that match your specification and production needs. Our injection molded parts are hand-vetted and built to last. Here are some other reasons why we are your one-stop plastic injection molding service provider in China:
1. Superior Quality Parts
Our team of seasoned operators and engineers strictly adheres to design, model, and production specifications, ensuring that we produce only the best. All of our parts undergo rigorous in-house quality control to guarantee top-tier quality.
2. Vast Experience and Expertise
With over a decade of experience and millions of parts manufactured across thousands of projects, our team has a wealth of knowledge and expertise in the manufacturing markets of both the USA and Europe.
3. Scalability and Precision
Scalability
Our concurrent product quality is maintained across all production scales, from a small run of one part to high-volume orders of 10,000+ parts.
4. Cost-Effective Solutions
We offer a complimentary design-for-manufacturability analysis to optimize design for cost efficiency. When producing high volumes, our injection molding process reduces waste and lowers the price per part, allowing our clients to maximize profits and minimize losses.
5. Quick Turnaround Times
Once tooling is completed, we can manufacture and deliver your parts within as little as seven days. Smaller orders may even have quicker lead times.
6. Low-Volume and Mass Production Capability
Injection molding is the most commonly used method for mass-producing plastic parts. In addition, low-cost aluminum tooling allows for the use of injection molding in prototyping and low-volume production.
7. Rapid Prototyping
Injection molding can quickly produce prototypes for rigorous testing, product marketing, concept validation, and more, allowing you to avoid expensive investments in mass production until your design is finalized.
Industries
Injection Molding Materials
Here's a reordered list of materials commonly used in plastic injection molding:
• Acrylonitrile butadiene styrene (ABS)
• Polycarbonate (PC)
• Polypropylene (PP)
• Polyethylene (PE)
• Polystyrene (PS)
• Polyethylene terephthalate (PET)
• Polyvinyl chloride (PVC)
• Nylon (PA)
• Acetal (POM)
• Thermoplastic elastomers (TPE)
• Liquid silicone rubber (LSR)
Finishing options
Comely CNC provides an array of finishing services to augment the beauty and cosmetic appearance of your part. We also have finishing options to increase the surface protection of your parts.
• Polishing:
We can achieve various finishes, including glossy, semi-glossy, matte, and mirror-like, by polishing and sandpapering the part to your desired specifications.
• Media blasting:
This technique uses a medium such as sand, bead, or glass to create a specific surface texture on the molded parts.
• Etching:
This process can be used to create inscriptions or markings on the surface of the molded parts.
• Custom:
We offer an array of custom finishing options that are unique or a combination of our standard finishes.
• Mill finish:
Parts are left in their natural state as they come out of the mold. This option is suitable for parts that will not be visible or used in closed areas.
• Painting:
Our injection-molded parts can be painted with automotive-grade wet paint or powder-coated in a range of colors and textures.
• Texturing:
This option can enhance the functionality of molded parts by improving their grip and hold.
• Pad printing:
We can transfer logos, graphics, and text onto the surface of the part using pad printing.
Plastic Injection Molding FAQs
1. What thermoplastics do you work with?
We work with high-quality engineering-grade thermoplastics, and virtually every type of thermoplastic can be processed into final parts.
2. What are the benefits of Injection Molding?
Injection-molded parts offer excellent cosmetic appearance, dimensional accuracy, strength, and high-performance. For large volumes of plastic parts, injection molding is the most cost-effective solution.
3. How long does it take to make my mold?
Tooling can take anywhere from 3 to 14 days, depending on the number of parts, design complexity, and material.
4. When can I receive the DFM for my part?
We provide the DFM free of charge when you request a quote.
5. How can you ensure my part works as specified?
We send 3-5 parts for testing and confirmation before molding the full order. We only proceed with molding after getting approval from the client. If the initial units are not satisfactory, we keep fixing the tool until the parts meet our customers' expectations.
6. Can I supply my plastics for molding?
Yes, you can supply your plastics for part molding, but please check with us to ensure that it is within our capabilities.