What is Die Casting
Die casting is a metal manufacturing process where molten metal is injected into a mold cavity under high pressure, and allowed to cool and solidify into a desired shape. The process is commonly used to produce small to medium-sized parts with complex shapes and high precision, typically made of non-ferrous alloys such as aluminum, zinc, and magnesium. Die casting offers a range of advantages, including high production rates, excellent dimensional accuracy, and the ability to produce parts with thin walls and intricate designs. The process is widely used in industries such as automotive, aerospace, electrical, and consumer goods.
Our Pressure Die Casting Processes
At Comely CNC, there are two main die-casting processes: hot chamber die casting and cold chamber die casting.
Hot Chamber Die Casting:
This process is used for alloys with low melting points, such as zinc, magnesium, and lead. In the hot chamber process, the molten metal is held in a furnace and pumped into the die cavity by a piston. The piston is submerged in molten metal, which eliminates the need for an external melting furnace. The process is suitable for small to medium-sized parts with simple designs.
Cold Chamber Die Casting:
This process is used for alloys with high melting points, such as aluminum, copper, and brass. In the cold chamber process, the molten metal is poured into a separate chamber, or shot sleeve, and then injected into the die cavity by a plunger. The plunger does not come into contact with the molten metal, which makes the process suitable for metals with high melting points. Cold chamber die casting is suitable for larger parts with more complex designs.
Both processes involve the same basic steps: melting the metal, injecting it into a die cavity under high pressure, allowing it to cool and solidify, and then ejecting the finished part from the die. The specific process used depends on the type of metal being cast and the size and complexity of the part being produced.
The steps of pressure die casting process typically include:
1. Preparation: The first step involves preparing the die casting machine, which includes installing the die, heating the die, and setting up the molten metal supply.
2. Injection: The molten metal is then injected into the die cavity at high pressure, using a plunger or piston. This forces the molten metal to fill the entire cavity and take on the shape of the die.
3. Cooling: Once the cavity is filled, the molten metal is allowed to cool and solidify into the desired shape. Cooling can be accelerated by spraying water or oil onto the die.
4. Ejection: Once the part has solidified, the die is opened, and the part is ejected from the cavity. Ejection can be done by a mechanical ejection system or by using air pressure.
5. Trimming: After ejection, the part may have excess material, such as flash or gates, that needs to be removed. This can be done using a trimming tool.
6. Finishing: The final step involves any necessary finishing operations, such as polishing, painting, or plating, to improve the appearance or function of the part.
The specific steps involved in pressure die casting may vary depending on the type of machine used, the material being cast, and the size and complexity of the part being produced. However, these basic steps form the foundation of the pressure die casting process.
Advantages of Pressure Die Casting
• High production rates:
Pressure die casting can produce large quantities of parts in a short amount of time, making it a cost-effective option for mass production.
• High dimensional accuracy:
The high pressure used in the process ensures that the final parts have excellent dimensional accuracy and consistency, with tight tolerances and smooth surfaces.
• Ability to produce complex shapes:
Pressure die casting can produce parts with complex shapes and intricate designs, including thin walls and internal features, that would be difficult or impossible to achieve with other manufacturing processes.
• Strength and durability:
The resulting parts have high strength and durability, making them suitable for applications where reliability and performance are critical.
• Versatility:
Pressure die casting can be used to produce parts from a wide range of materials, including aluminum, zinc, magnesium, and copper alloys.
• Cost-effective:
The high production rates, low scrap rates, and minimal need for post-processing make pressure die casting a cost-effective option for manufacturing high-quality parts.
Die Casting Applications
• Precision parts
Die casting is used for making precision parts that have critical requirements around weight, dimensions, thin walls, tight tolerances, and even cosmetic finish. Normally, the die casting parts would have a post-machining for some critical areas. Die casting is applied in aerospace, automotive, and engineering industries to make parts that must match specifications to ensure functionality and precision in operations.
• Mass production
Die casting can make large parts and even larger volumes of parts. The process is mostly applied to mass production operations where cost can be spread over more volume, and the cost per part is relatively reduced. This is one of the reasons why die casting operations can help improve the profitability of your parts.
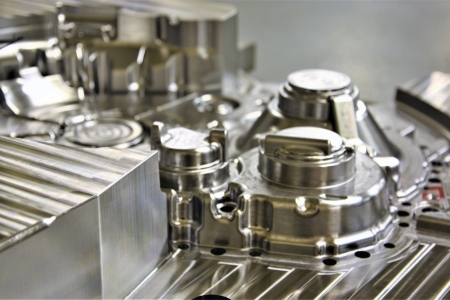
Applications of Die Casting
Comely CNC pressure die casting operations can be used in any of the following industries:
• Aerospace
Die casting is commonly used in the aerospace industry to produce lightweight and high-strength components such as turbine blades, engine casings, and landing gear components.
• Energy and Power
Die casting is used in the energy and power industry for producing components such as heat sinks, enclosures, and housings for power distribution equipment.
• Industrial
Die casting is used in various industrial applications for producing components such as pumps, valves, and gears.
• Automotive
Die casting is widely used in the automotive industry for producing parts such as engine blocks, transmission cases, and suspension components.
• Consumer Products
Die casting is used in the production of consumer products such as computer hardware, connectors, housings for electronic devices, and household appliances such as refrigerators, washing machines, and vacuum cleaners.
• Construction
Die casting is used for producing components for the construction industry such as window frames, door handles, and brackets.
• Robotics
Die casting is used in the production of robots and robotic components such as motor housings, gears, and structural components.
Material options for Die Casting:
• Aluminum:
It is the most commonly used material for die casting due to its lightweight, high strength, and excellent thermal and electrical conductivity.
• Zinc:
It is another popular choice for die casting due to its excellent dimensional stability, corrosion resistance, and easy machining capabilities.
• Magnesium:
It is a lightweight material with excellent strength-to-weight ratio, making it suitable for producing complex, lightweight components.
• Copper:
It is used in die casting for its high electrical conductivity and thermal conductivity, making it ideal for heat sinks and electrical components.
• Brass:
It is an alloy of copper and zinc, and is commonly used in die casting for decorative and architectural purposes due to its excellent corrosion resistance and aesthetic appeal.
• Lead and Tin:
These materials were commonly used in the past for die casting, but due to their toxicity and environmental concerns, their use is now limited.
Finishing Services
Comely CNC provides a range of finishing solutions for metal castings that enhance both the cosmetic appearance and performance of the parts. These finishing techniques are applicable for pressure die casting and include:
• Plating
• CNC machining
• Painting
• Sanding
• Polishing
• Standard
• Anodizing
• Sandblasting
• Powder coating
Why Comely CNC
Comely CNC offers optimized pressure die casting solutions to produce high-performance parts that meet our clients' needs. Here are the advantages of choosing our services:
• Quality and Consistency:
We prioritize quality throughout the production process, ensuring consistent, high-quality end-use products.
• Cost and Profitability:
Our competitive pricing adds value to clients' businesses by delivering parts at a lower cost-per-part, making us one of the most competitive manufacturing businesses in China.
• Shorter Lead Times:
With optimized pressure die casting services and in-house capacity, we deliver products faster with shorter lead times.
• One-Stop Shop:
Our one-stop-shop approach streamlines the product development cycle, providing comprehensive services from design to finishing solutions that enhance the appearance and functionality of the final product.
Die Casting FAQs
1. When will I receive the DFM for my part?
We provide the DFM free of charge when sending a quote.
2. How do you ensure that my part will work as specified?
We send 3-5 parts to our clients for testing or confirmation before producing the full order. We only mold all the parts after receiving approval from the client. If the initial units are not up to expectations, we will continue to fix the tool until the parts are accepted by our customers.
3. How long can you store our tooling before the next order?
We can store your tooling for up to 5 years after the last order.
4. What if our tooling breaks before the expected quantity is molded?
If the tooling has reached the end of its tooling life, we can make a new mold for you free of charge.