What is Rapid Tooling
Rapid tooling is a process used to quickly produce molds for low-volume injection molding of plastic parts. It is also known as bridge tooling or prototype tooling. Rapid tooling techniques typically involve using 3D printing or CNC machining to create a mold from aluminum or steel. Once the mold is created, it can be used to produce multiple copies of a part using injection molding. This is an effective way to produce functional prototypes quickly and at a lower cost than traditional tooling methods. Rapid tooling is often used to bridge the gap between prototyping and high-volume production, providing a cost-effective solution for producing small to medium quantities of parts. Rapid tooling is also flexible, allowing for design changes to be made quickly and easily during the prototyping phase.
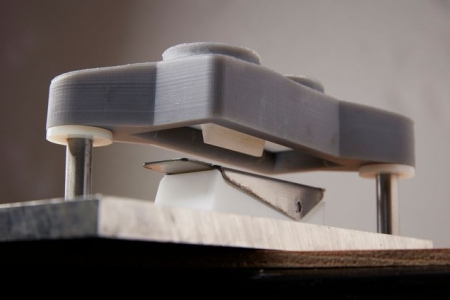
Advantages of Rapid Tooling
• Faster production:
Rapid tooling allows for the creation of molds and tooling in a fraction of the time required by traditional manufacturing methods. This enables faster product development and quicker time-to-market.
• Reduced costs:
Rapid tooling eliminates the need for expensive tooling machinery and manual labor, reducing costs associated with production. Additionally, it enables companies to produce small quantities of parts cost-effectively, making it ideal for low-volume production.
• Improved accuracy:
Rapid tooling techniques use computer-aided design (CAD) software and 3D printing technologies, which ensure precision and accuracy in the final product.
• Increased design flexibility:
Rapid tooling enables designers to make changes to the product design quickly and efficiently, making it easier to modify the mold or tooling as needed.
• Reduced waste:
Rapid tooling techniques use additive manufacturing technologies that produce little to no waste, making it an environmentally friendly option.
• Enhanced customization:
Rapid tooling enables companies to produce customized parts and products with unique features and designs that are difficult or impossible to achieve with traditional manufacturing methods.
Options for Rapid Tooling
• Aluminum
Aluminum molds are cost-effective and provide dimensional stability due to their even heat dissipation, resulting in reduced deformation and less waste. They can reduce tooling costs by 16-30% and cycle times by up to 35%, but have a shorter life cycle and are not suitable for high-volume processes.
• Steel
Steel molds are sturdy and ideal for high-volume production, with a longer life cycle than aluminum. They are suitable for producing molds from engineering-grade plastics but are more expensive and take more time to produce molds and prototypes.
Applications of Rapid Tooling
• Automotive:
Rapid tooling is employed to manufacture various parts and components, including dashboard components, engine parts, and door handles
• Aerospace:
Rapid tooling is used to produce aircraft components, such as wing structures and turbine blades.
• Medical:
Such as prosthetics, surgical instruments, and orthopedic implants, are manufactured using rapid tooling in the medical field.
• Consumer goods:
Rapid tooling is utilized to produce consumer products, such as toys, electronics, and appliances.
• Packaging:
Such as bottles, containers, and lids, are manufactured using rapid tooling in the packaging industry.
• Industrial equipment:
Rapid tooling is used to produce industrial components, such as gears, valves, and bearings.
• Jewelry:
Customized and unique jewelry designs are manufactured using rapid tooling in the jewelry industry.
Why Comely CNC?
• Streamlined process flow
At Comely CNC, our operations follow a dedicated process flow that minimizes risk, verifies raw materials, and ensures the production of high-quality prototypes and end parts consistently.
• Quick turnaround
Leverage our industrial-grade equipment to accelerate your product development cycles and hasten your time-to-market. With our expertise, we can help you overcome bottlenecks and fast-track your product development right away.
• Scalable and consistent manufacturing
Our additive manufacturing solutions prioritize scalability and repeatability, providing you with the flexibility to prototype or manufacture according to your budget without compromising print quality.
• Comprehensive finishing services
In addition to our precision printing capabilities, we also offer finishing solutions to enhance the aesthetic appeal of your parts. Our in-house finishing services are subject to the same stringent quality control measures for a lasting guarantee of quality.
• Quality and Consistency
We prioritize quality throughout the production process, ensuring consistent, high-quality end-use products.
• Cost and Profitability
Our competitive pricing adds value to client's businesses by delivering parts at a lower cost-per-part, making us one of the most competitive manufacturing businesses in China.
• One-Stop Shop
Our one-stop-shop approach streamlines the product development cycle, providing comprehensive services from design to finishing solutions that enhance the appearance and functionality of the final product.